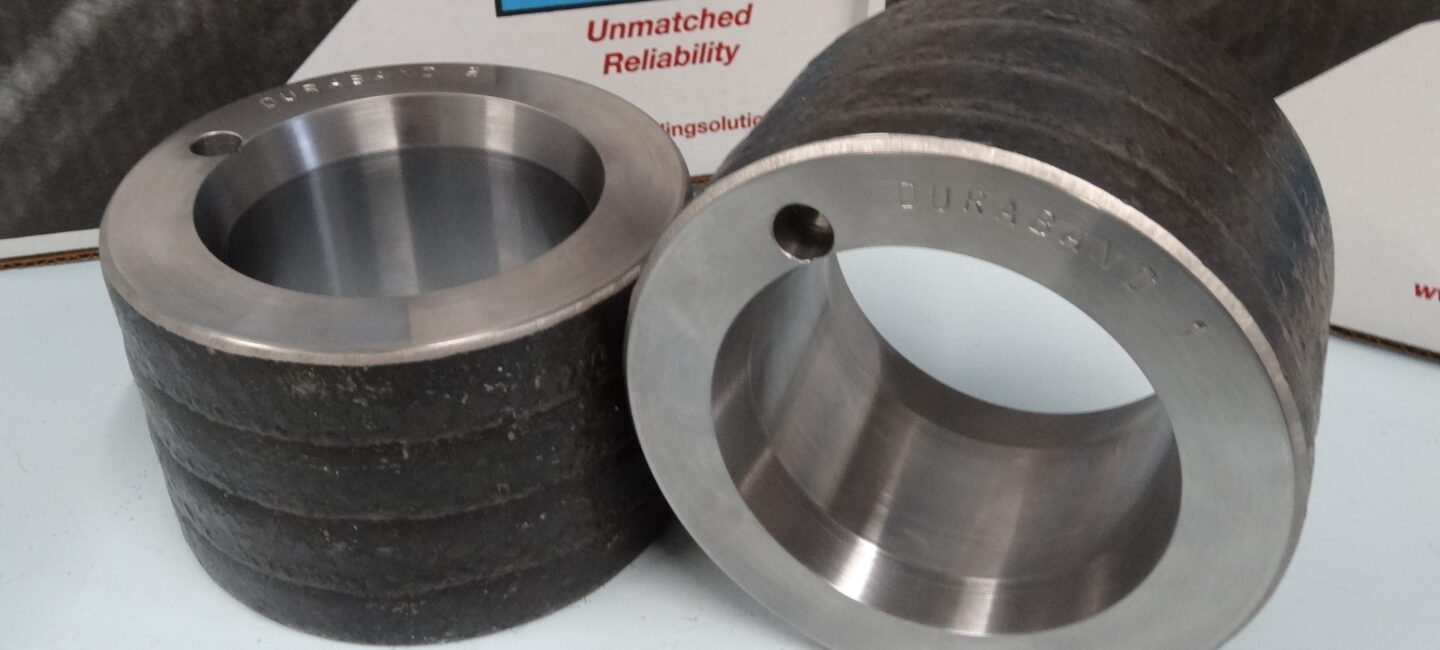
Protección de carcasa
Discusión sobre la historia de las pruebas de desgaste de la carcasa
Los materiales de hardbanding, aplicados mediante un proceso de soldadura a las uniones de herramientas de la sarta de perforación, se desarrollaron principalmente para brindar protección contra el desgaste abrasivo. Los propietarios de la sarta de perforación quieren que sus activos alcancen la mayor cantidad de horas de perforación posible sin que se rebajen o desechen por pérdida de espesor de pared. Al mismo tiempo, prevenir el desgaste del casing causado por el contacto con la sarta de perforación es una prioridad para el operador, quien tradicionalmente es el dueño del casing. Las pruebas de desgaste de la tubería de revestimiento de terceros han evolucionado para garantizar que tanto la sarta de perforación como la tubería de revestimiento pueden protegerse con la elección correcta del material de endurecimiento superficial, explica Colin Duff, director global de Soluciones de endurecimiento superficial.
En décadas pasadas, cuando los perfiles de los pozos se desviaban más, lo que generaba un mayor contacto entre la sarta de perforación y el revestimiento, existía la preocupación de que una junta de herramienta de la tubería de perforación pudiera causar tanto desgaste como para perforar el revestimiento. El primer programa de prueba para investigar el daño potencial a la carcasa fue desarrollado por un laboratorio externo en Texas, EE. UU., a principios de la década de 1990. En ese momento, la prueba de desgaste de la carcasa se denominaba 'DEA 42'.
Se crearon nuevas aleaciones de hardbanding, como Duraband NC®, que protegerían la unión de la herramienta contra el desgaste y, al mismo tiempo, tendrían una relación de baja fricción cuando giran contra la carcasa. Anteriormente, en pozos más verticales, el hardbanding consistía en carburo de tungsteno colocado en una matriz simple de acero dulce. Si bien esta aplicación fue efectiva para proteger las juntas de la herramienta del desgaste, fue extremadamente abrasiva contra la carcasa y actuó como una herramienta de mecanizado.
En el programa de prueba inicial en el que se probaron juntas de herramientas, nuevos materiales de endurecimiento superficial y revestimiento de carburo de tungsteno, los resultados enumeraron valores como "Factor de fricción" y "Factor de desgaste". Para ser aprobado como hardbanding "compatible con la carcasa", el factor de desgaste tenía que estar por debajo de un valor de 2,0. Un valor superior a 2,0 se consideró un fracaso.
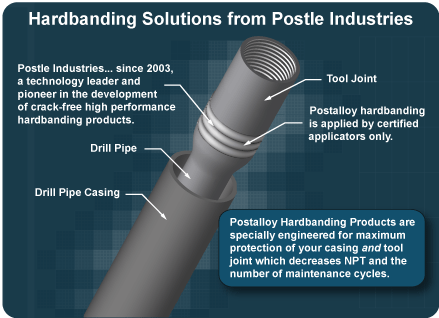
Luego, el equipo de prueba se vendió a otro laboratorio. Después de algunas pruebas iniciales, los nuevos ingenieros determinaron que los resultados de las pruebas no eran consistentes. Esto se debió al tipo de carcasa utilizada en muchas de las pruebas. La especificación de la carcasa permitía una amplia gama de propiedades del material, lo que aumentaba la falta de fiabilidad de los resultados comparables. Además, la carga lateral utilizada en la prueba no fue uniforme ni estable. Por lo tanto, se realizaron varias mejoras en el equipo para mejorar la repetibilidad de los resultados.
Los operadores de petróleo y gas me han preguntado, preocupados por el desgaste de su carcasa, si existe alguna correlación entre la prueba de desgaste de la carcasa anterior y la actual. La respuesta es que simplemente no hay correlación entre los resultados de la prueba. Sin embargo, en varias especificaciones de prueba con el equipo y el procedimiento mejorados, Duraband NC ha demostrado una baja fricción constante contra la carcasa, lo que causa alrededor de un 50 % menos de daño que una junta de herramienta sin endurecimiento superficial. Las aplicaciones de carburo de tungsteno destruirían la muestra de la carcasa antes de la conclusión de la prueba.
Aparte de los resultados de las pruebas de desgaste de la carcasa, otra consideración importante para proteger la carcasa es usar un material de banda dura que no tenga grietas. Si un hardband se agrieta, existe un mayor potencial para que se “astille” en pedazos en el fondo del pozo. Las piezas afiladas de aleaciones de metales muy duros pueden quedar atrapadas entre la sarta de perforación y el revestimiento y causar daños importantes. Esta es una de las razones por las que nuestra prioridad con el desarrollo de Duraband NC fue que se aplicaría y volvería a aplicar 100 % libre de grietas cada vez.
Finalmente, el tipo de lodo utilizado durante la perforación influye en cuánto desgaste se observa tanto en la sarta de perforación (hardbanding) como en la tubería de revestimiento. Se sabe que el lodo a base de aceite o sintético reduce el desgaste. A medida que más organizaciones eligen cambiar a lodo a base de agua debido al elevado costo del lodo a base de aceite, notan un aumento en el desgaste. En la misma prueba de desgaste de la carcasa donde otros parámetros son iguales, vemos una diferencia significativa cuando se cambia el tipo de lodo.
Hoy en día, la única protección comprobada y eficaz contra el desgaste de la tubería de revestimiento es tener un endurecimiento protector orgulloso y amigable con la tubería de revestimiento, como Duraband NC, aplicado a las uniones de la herramienta y las almohadillas de desgaste centrales de la sarta de perforación.
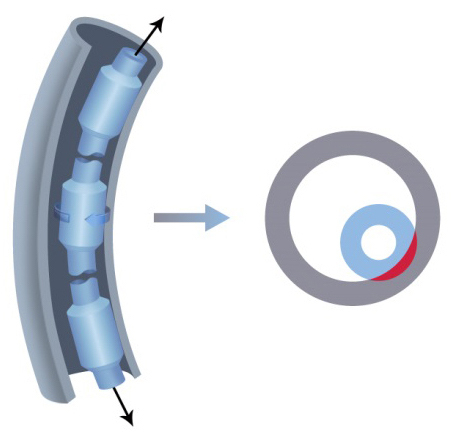
Cómo la sarta de perforación entra en contacto con la tubería de revestimiento
Comparación de los resultados de las pruebas de desgaste de la carcasa de hoy
Hay más de una especificación de prueba disponible con diferentes parámetros, por lo que es importante tener en cuenta las condiciones de prueba exactas al comparar productos de endurecimiento superficial con respecto al desgaste de la carcasa. Hay varias variables permitidas por la prueba que deben ser consideradas cuando se comparan los resultados.
Las variables incluyen:
• Tipo de lodo (sintético o a base de agua) utilizado para la prueba
• Fuerza de carga lateral (3000 lb, 5000 lb o 7000 lb)
• Tipo de carcasa utilizada para la prueba (N80, T95, Q125)
Duraband NC está aprobado por NS-1 para la primera aplicación y la reaplicación sobre sí mismo y otros materiales. Ha sido aprobado para su uso por casi todas las principales empresas mundiales de producción de petróleo y gas en todo el mundo. Estos operadores reconocen la importancia de utilizar endurecimiento superficial sin grietas que no dañe la tubería de revestimiento para proteger la sarta de perforación sin dañar la tubería de revestimiento.