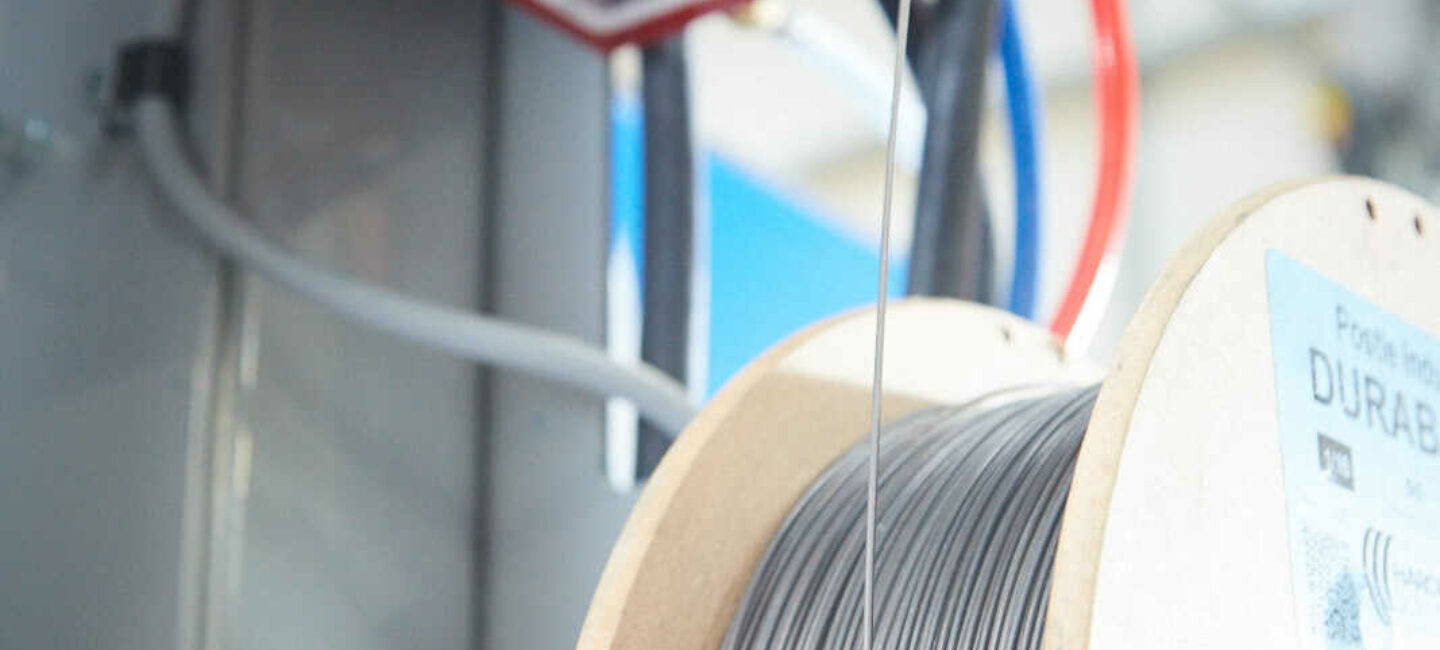
Application Essentials
How do we ensure hardbanding is applied safely, and the drill pipe owner gets maximum protection for the life of their drill pipe? In welding terms, hardbanding is relatively simple. If you have the correct material, the operator has been trained properly, the equipment is precise and consistent, and the correct procedure is followed, then excellent hardbanding is not difficult. At Hardbanding Solutions our aim is to make the need for hardbanding removal history. Not only does it save our industry time and money, but it leads to safer and more efficient drilling.
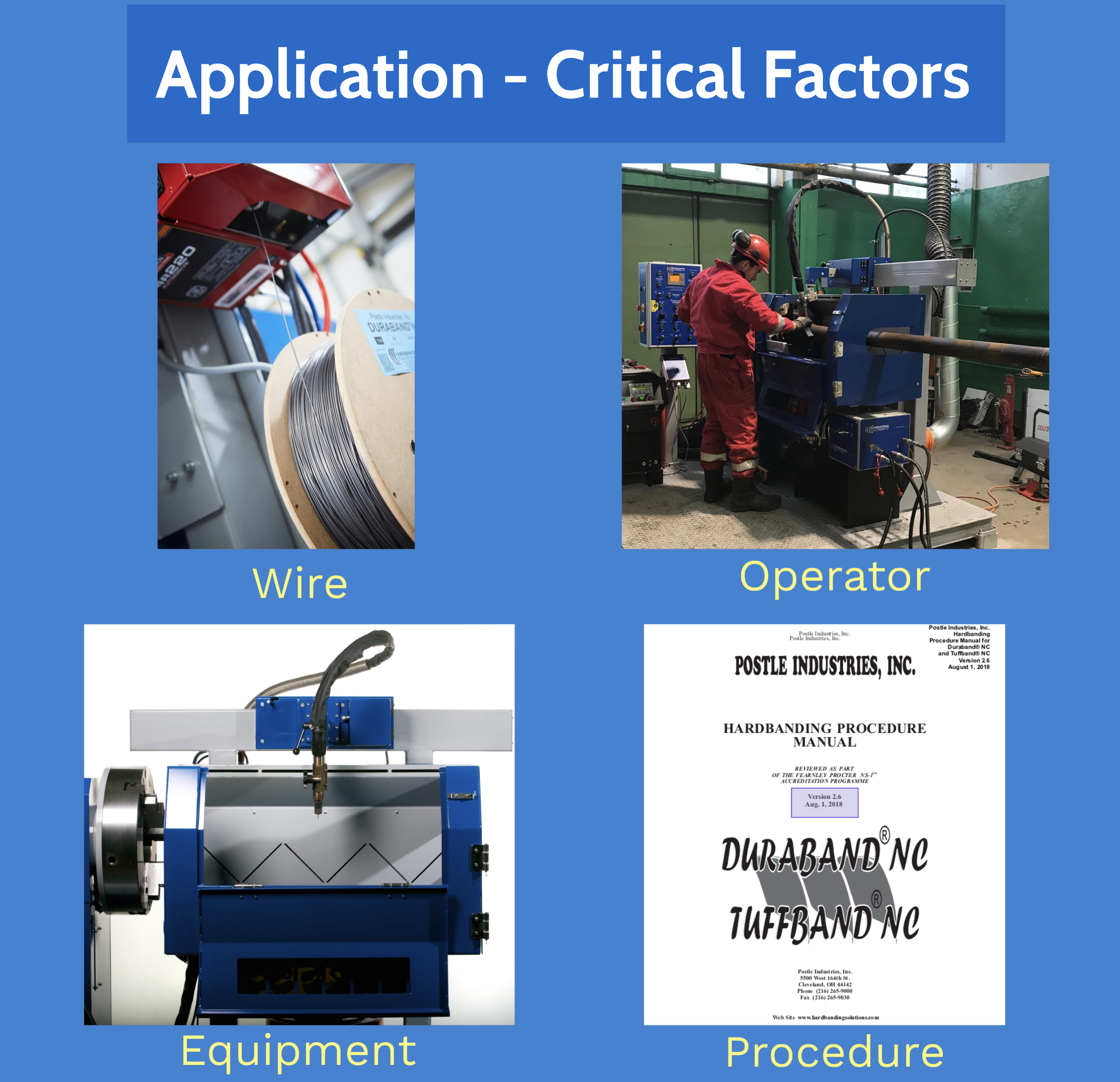
Application Essentials
Good record keeping
We encourage our applicators to keep detailed records of each job. Then, if something goes wrong they can be consulted to determine the correct procedures were followed.
- IPC condition
- Wire being applied – Lot Number
- Condition of old hardband
- Pre-heat temperature
- All welding parameters
- Interpass temperature
- Finished hardbanding
- Band height, shape, width and condition
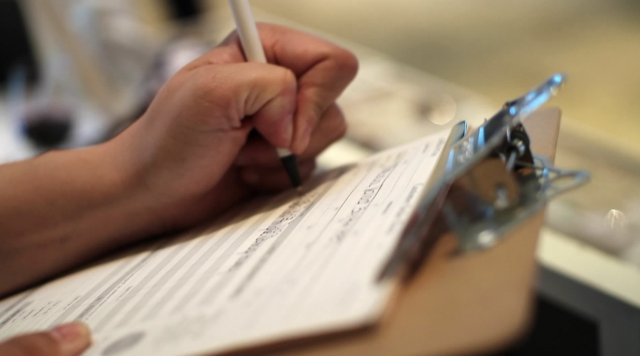
Pre inspection
Making sure the tool joint is ready for application or reapplication is essential. For example, on a new tool joint we must be certain all phosphate has been removed, as well as any other contaminants such as oil. Inspection is even more important before reapplication over a previously worn hardband.
Unfortunately, due to the chemistry of some materials still on the market today, and mistakes during application, some hardbands will need to be removed and are not candidates for direct reapplication. This can be due to incompatible chemistry or defects.
Here are some defects to look out for. Voids, porosity, cracking and delamitation. Please contact us for advice, we're happy to help with any application to make sure it's done safely.
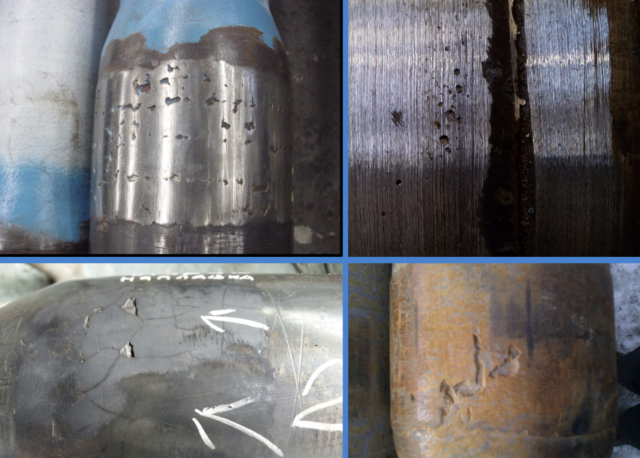
Cleaning
The best tool to remove contamination such as dirt or oil from the tool joint is with a grinding stone or flap disc. We do not recommend using wire brush type tools.
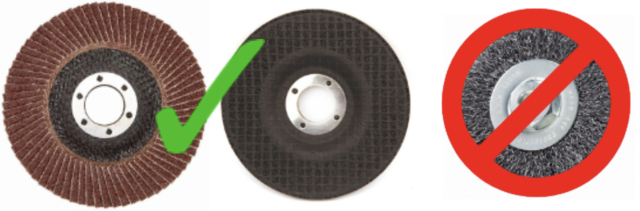
Preheating
Preheating – the part of hardbanding most often skipped and misunderstood. The reason for preheating before welding is to ensure the area around and under the weld is at sufficient temperature after application to aid slow-cooling. If the base material is cooled too quickly, then the heat affected zone, or HAZ, will become too hard. By ensuring a high final interpass temperature by combining preheat and heat added by the welding process itself, and applying protection like the Hardbanding Solutions Insulator, the tool joint will cool slowly and the HAZ will not harden beyond a safe level.
It's important to achieve a soak heat while preheating, meaning the heat must have permeated through the wall thickness of the tool joint. If only the surface is heated, the tool joint will cool too quickly. To find out how to determine a soak heat, contact us or consult our Duraband NC manual.
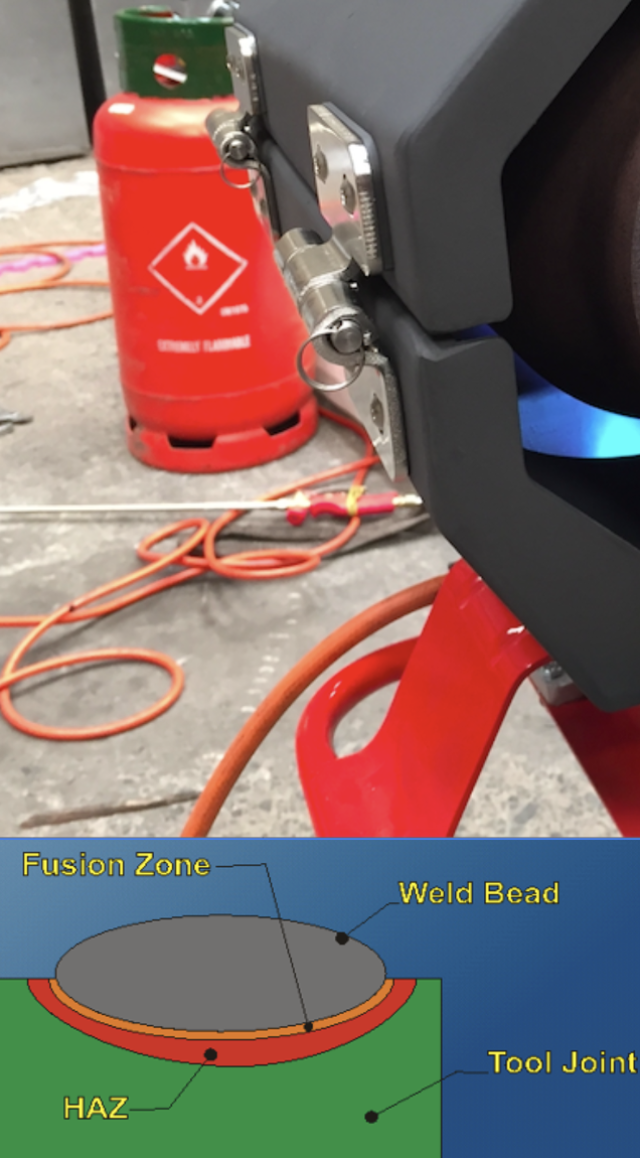
Preheat methods
The equipment used to preheat will have an impact on the time and attention needed to ensure success. Propane is the most common method. We do not recommend using an open flame as it's difficult to achieve a soak heat. Much better is a preheat box like our own SkyeHeat. Induction heating is by far the easiest and fastest method, but it comes with a higher up-front cost.
When measuring the final interpass temperature after welding, the measurement should be taken on the base material, within 1" of the hardband. We do not recommend using temperature sticks, as these are not precise enough. Digital pyrometers are ok but should be used with caution as bright surfaces can alter the readings. By far the best method is a probe or contact thermometer.
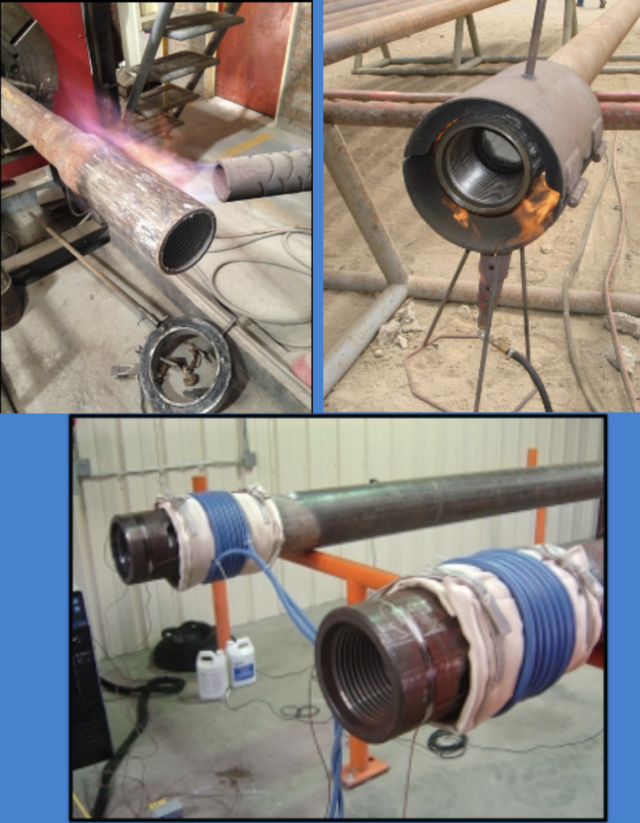
Welding
The welding procedure itself is relatively simple, as long as the welding equipment is sufficient. Welding machines come in all shapes and sizes. We had been training hardbanders across the globe for years before we decided to design our own Skye hardbanding unit, to make hardbanding easier. We had found some units built for a cheaper price were actually incapable of applying hardbanding as good as it should be. It normally takes between 6 and 10 minutes to apply three bands. Controlling the heat in the tool joint throughout is important, we don’t like welders taking a break while a hot pipe is lying!
- Ensure the recommended welding parameters are being followed.
- Weld area must be at the recommended temperature at the start of welding.
- Hardband operator must closely monitor process and make adjustments as necessary.
- Unload pipe and quickly check interpass temperature, hardband O.D. and width.
- Apply slow-cooling protection immediately.
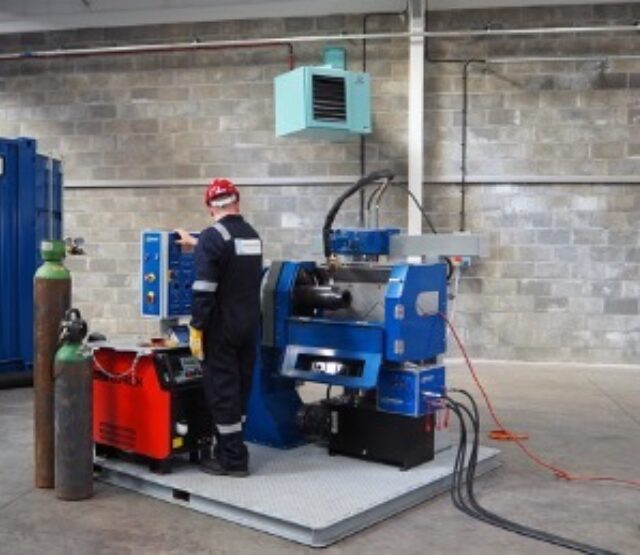
Post inspection
The finished hardband should be inspected to make certain it conforms to the material and customers acceptance criteria. With Duraband, the following should be verified.
- No voids, cracks, or other defects.
- Bands should be flat or slightly crowned.
- Concave bands are not acceptable.
- Good tie-ins (10-15% overlap).
- Correct band height - 3/32" to 5/32" (2.4mm to 4.0mm).
- Bands start approximately 3/8" (10mm) from 18° taper.
- Approximately 3” (75mm) total width.
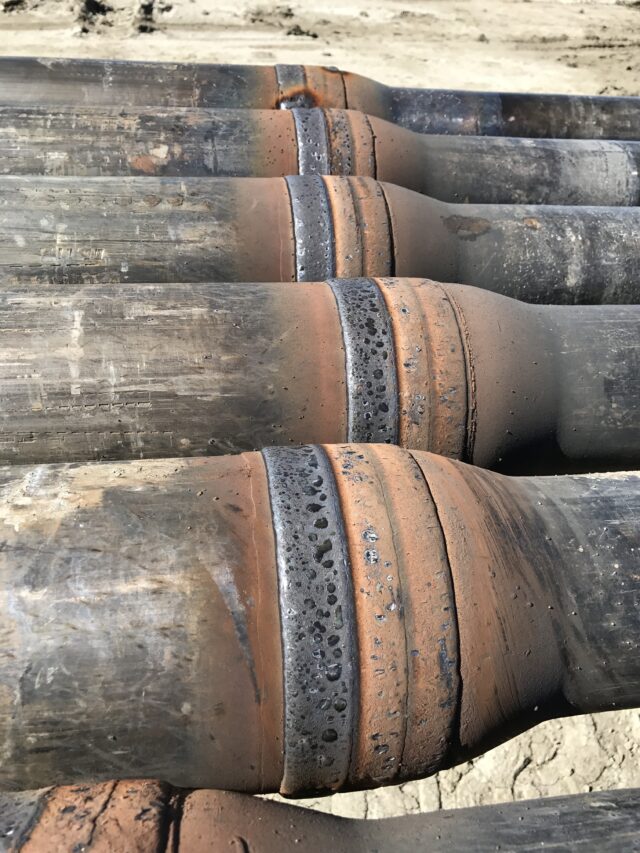