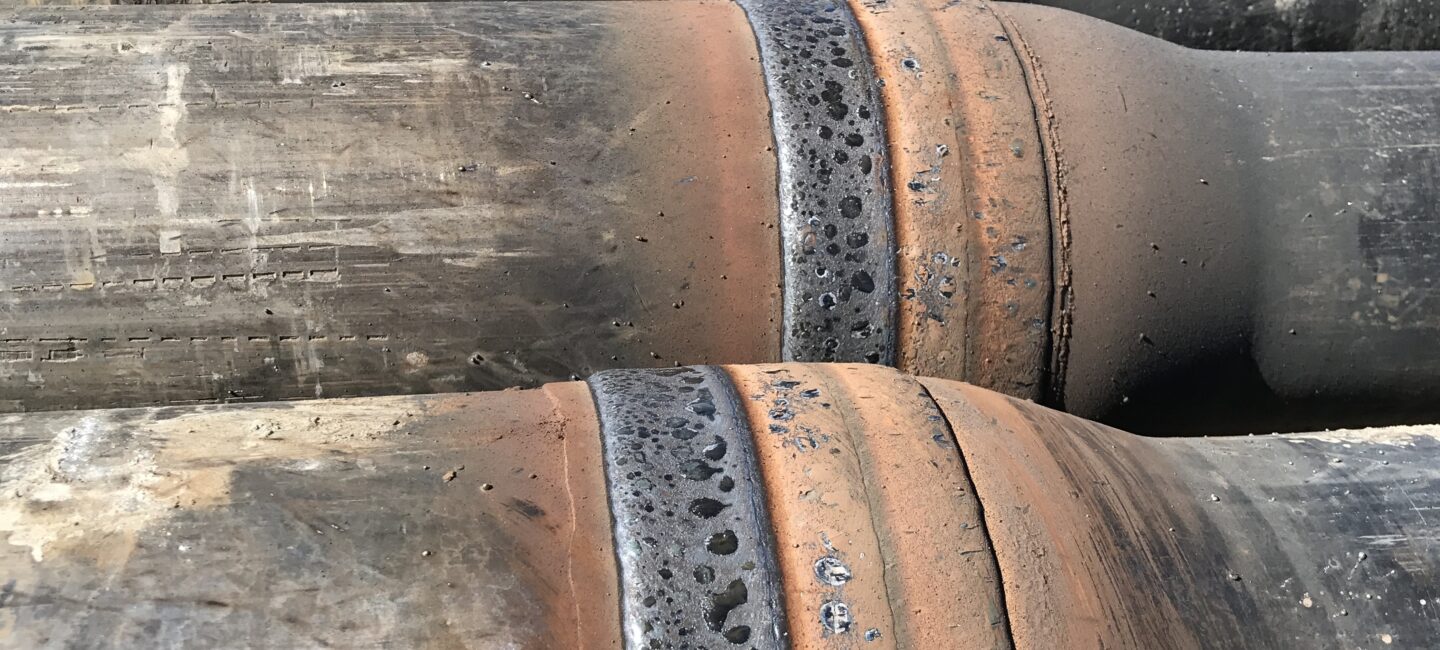
Hardbanding Essentials
The 3 Goals of Hardbanding
The primary reason for hardbanding is to protect the drill string from wear. The weld (hardband) is a hard, long wearing material that is designed to wear instead of the connection. It is a sacrificial weld that should have the ability to be reapplied many times, greatly extending the life of the tubular it's designed to protect. When managed properly, wear of the tool joint connection or center wear pad is eliminated.
Another goal of hardbanding is to prevent casing wear. With the spinning and dragging motion of the tubulars there is abrasive contact with the casing wall. Hardbanding creates a surface that is considerably more casing friendly. Casing wear from an unprotected tool joint is more than double the wear from a tool joint protected by Duraband. It is important to note that not all “casing friendly” hardbanding materials offer equal protection.
The third and most forgotten goal of hardbanding is reliable reapplication. For too long our industry has been offered materials which will work well on first application but fail when the more metallurgically challenging reapplication takes place. Hardband removal should be a thing of the past.
Application
Hardbanding is typically applied in 3 x 1” wide bands on the box tool joint of drill pipe. It can also be applied to the pin end when tool joints are long or drilling conditions are particularly abrasive. The number of bands applied on HWDP and Drill Collars varies. The positioning of the bands is deliberate, to ensure the hard material does not interfere with elevators and there is an area left for tong space. Tongs don’t like hardbanding and can be damaged if they connect with it.
This is how the application looks. Here the second band is being applied beside the first, the tool joint is rotated while the welding torch oscillates and puts down the hardband wire.
Drill String Protection
We can measure the simple abrasion resistance of any metallic layer by conducting a G65 wear test. Every hardband wire is different, and the results we get depend on the chemistry of that particular product. Hardband chemistry is important not only for abrasion resistance, but it has other implications. For example tungsten carbide provides excellent wear resistance, but at the same time is extremely abrasive on casing and acts as a cutting tool. In higher percentages some elements included for hardness, such as boron, can eventually lead to cracking. It should be noted that hardness is not always a good indication of wear resistance.
Some of the most common chemical elements used in hardbanding materials are:
- Niobium (or columbium)
- Chromium
- Titanium
- Boron
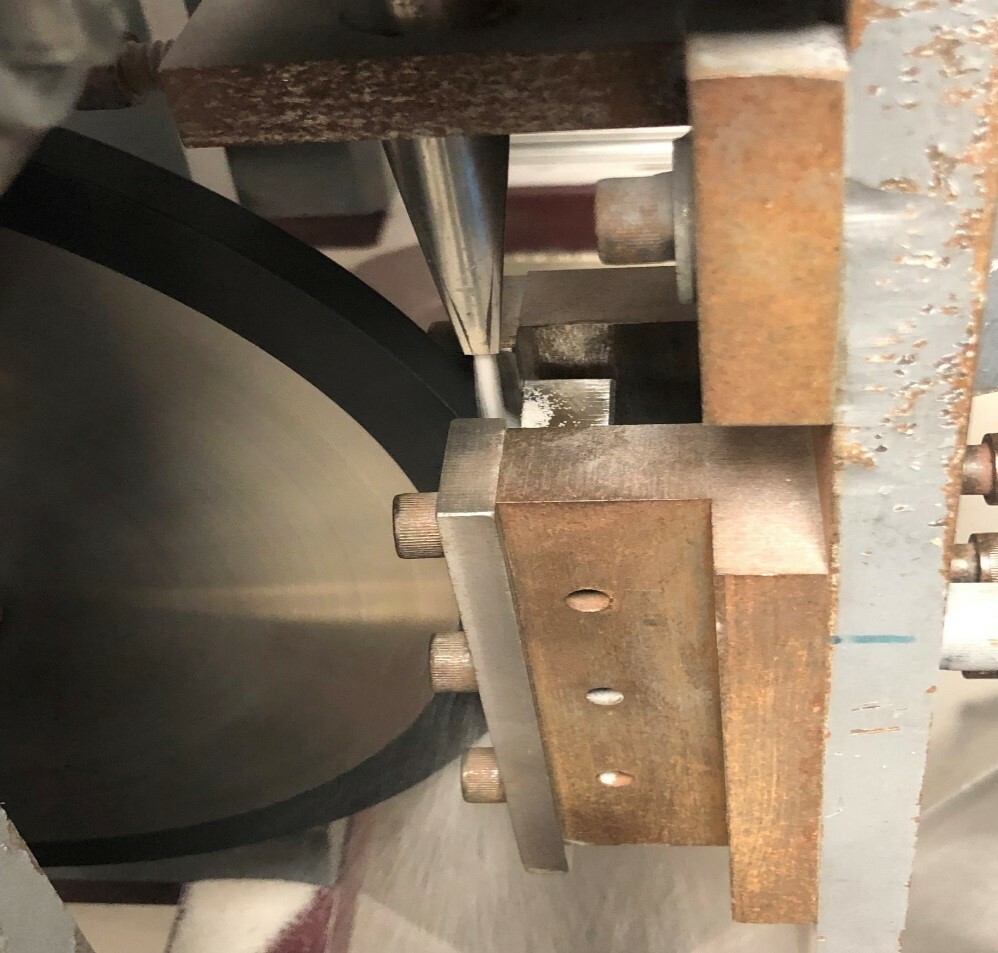
The ASTM G65 wear test is used to compare the abrasion resistance of metal alloys
Casing Protection
Comparative casing wear can also be measured in the laboratory. The industry standard test for this has evolved over the years, so caution must be taken when comparing results (see more here). In general, Duraband NC will cause about 50% less wear to the casing than a bare tool joint in the same test. The materials chemistry is formulated to have a low friction relationship when it comes into contact with all grades of casing. The most beneficial application type is proud. If hardbanding is applied flush (in a recess) to reduce outside diameter of the connection, the application is no longer casing friendly (and the tool joint will wear as the hardband wears). In recent years some operators have insisted the hardbanding is ground to a specified smoothness before going downhole to reduce the initial wear, although this may only be required in unusual circumstances.
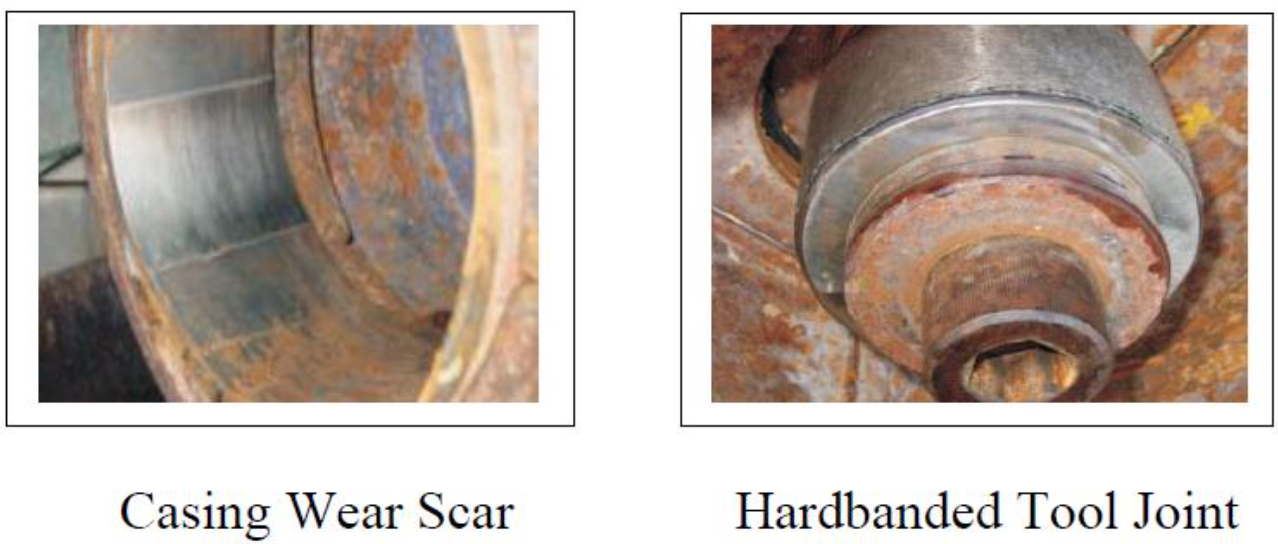
Typical casing wear test set-up.
Reliable Reapplication
The effects of dilution
Here is a tool joint that has come back from the well and the hardbanding has worn. The hardbanding has done its job, if it wasn’t there this tool joint would likely be damaged beyond repair. Even when worn flush, hard material remains, as you can see in the cross section. When the proud portion is worn off and the tool joint comes back for reapplication, the material we reapply is being diluted by the previous weld chemistry underneath. When hardbanding reapplication goes wrong, when it cracks and spalls, it is more often down to wire chemistry rather than the wrong welding procedures being used.
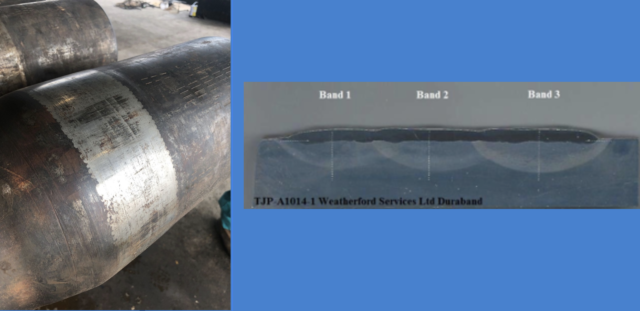
In fact, during the first application of hardbanding onto the new tool joint, the weld layer can be as much as 40% base material. This does not mean the hardbanding like Duraband NC is only 60% effective; the balanced chemistry means the wear characteristics remain. In subsequent reapplications on the same tool joint, the percentage of hard material in the matrix grows. This can be beneficial in a stable material like Duraband. However it can be the trigger for problems like cracking and spalling with some other materials where unstable chemical elements become more abundant in the matrix.
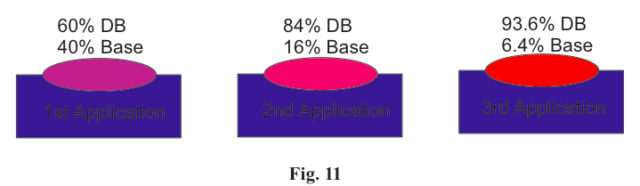