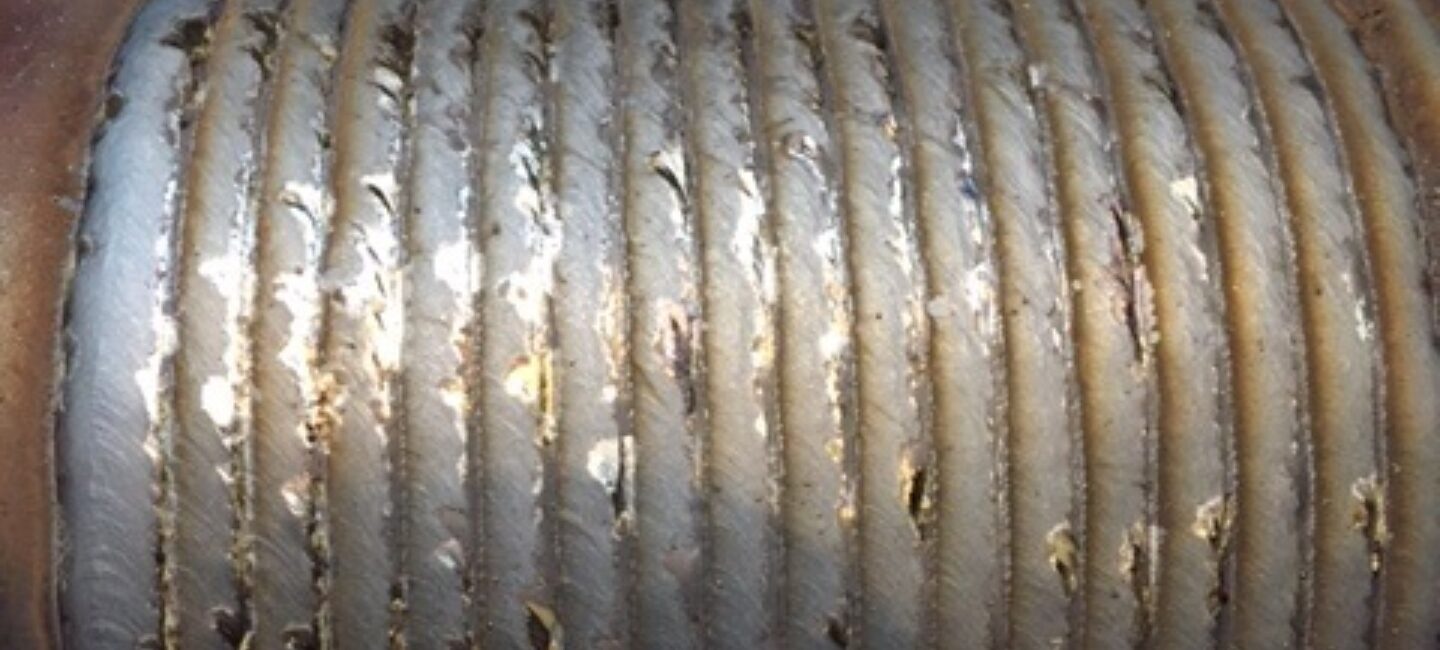
Coolbanding to Protect IPC
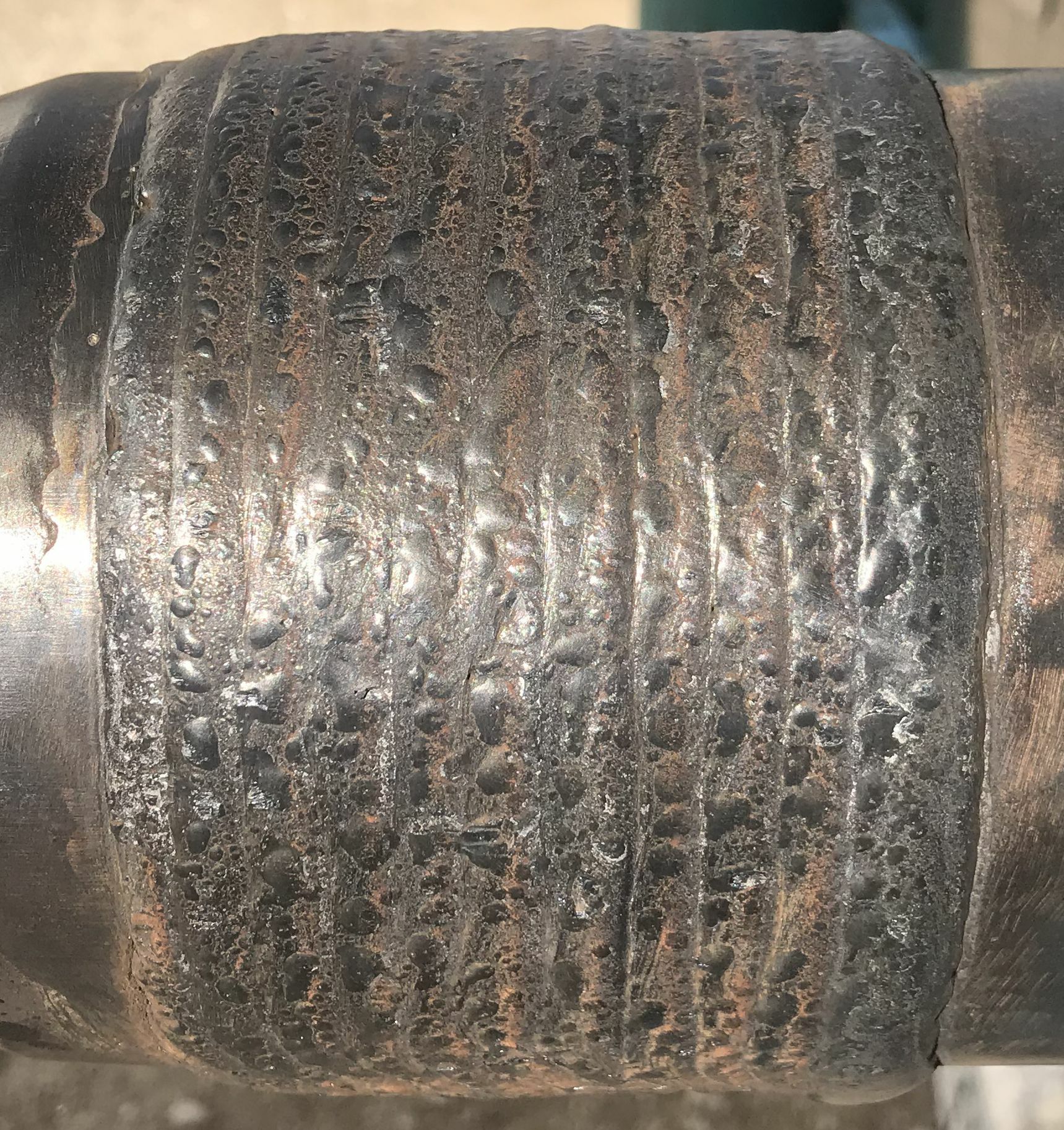
An application of coolbanding
CoolBanding - Low Heat Input Hardbanding
U.S. Pat. No. US 10,267,101 B2
During conventional hardbanding re-application procedures, the tool joint is preheated from 225°F to 700°F (107°C to 371°C) depending on the tool joint OD, hardbanded and then slow cooled. During the hardbanding procedure the temperature of the tool joint can easily rise to 600°F to 850°F (315°C to 454°C). In nearly all instances of the re-applications the internal plastic coating (IPC), if present, is burned out or seriously damaged. This has serious implications to the drilling operation. To replace the IPC is time consuming and costly.
In attempt to keep the tool joint cool, some applicators elected to lower preheat temperatures only to find that they have seriously compromised the ductility of the tool joint by essentially quenching it. They also found that they are outside of some required specifications. Others have applied using water cooling in various ways, but the outcome of poor ductility and specification non- conformance is still the same. In light of the challenges described above, Hardbanding Solutions by Postle Industries set out to develop a hardbanding procedure that accomplishes the protection of the IPC, while maintaining tool joint integrity. The result is a patented procedure aptly named CoolBanding. This procedure can be used with a variety of IPC products with excellent results. Preheated water cooling is a requirement for the CoolBanding procedure.
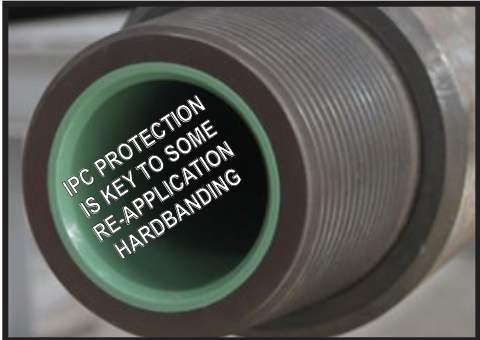
It should be noted, that while preserving the IPC is desirable, there is no known specification that requires that the tool joint ID to be plastic coated.
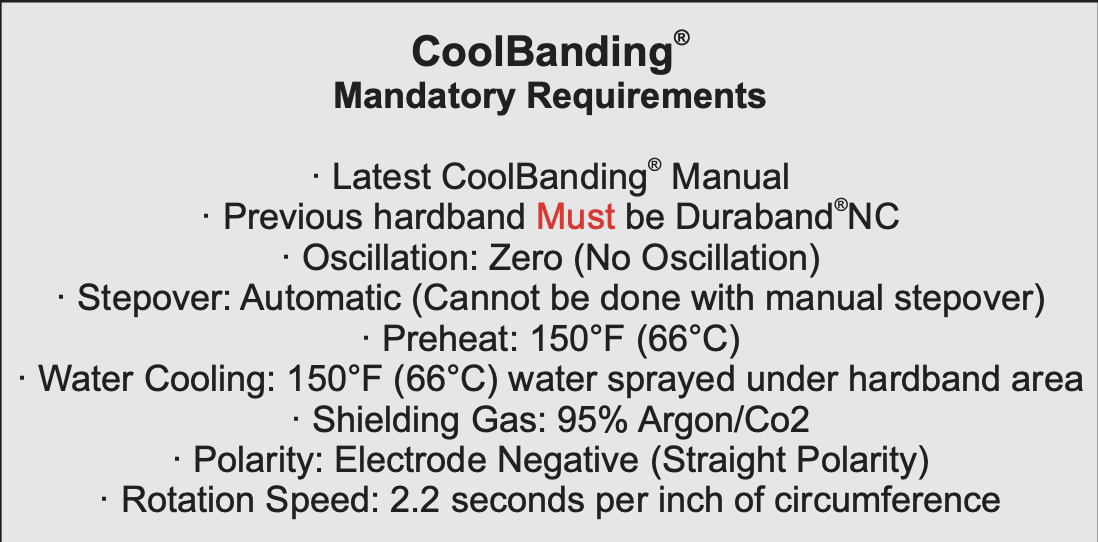
A thorough inspection of the IPC previous to CoolBanding will help ensure successful outcomes. The CoolBanding Manual does not address nor guarantee successful re-applications to protect the IPC. It is strictly a guideline to produce low heat input to the inside diameter of a tool joint, which when properly applied, can result in protecting the IPC from welding arc heat.
The hardbanding industry has long followed strict procedures of re-application hardbanding that specified minimum criteria for preheats and interpass temperatures. These specifications were written to ensure that the hardbanding weld deposits would cool slowly enough to prevent excessive high base metal heat affected zone (HAZ) hardness values and potential cracking. Typical preheats ranged from 150°F to 600°F (66°C to 316°C) and were determined strictly by tool joint outside diameters. While this procedure, coupled with slow cooling procedures ensures base metal HAZ hardness levels below the specified requirement of 40Rc, it did little to keep the tool joint inside diameter cool enough to prevent the IPC from heat damage. Generally speaking, most IPC products start to deteriorate by hardbanding procedures at about 400°F (204°C), which in many cases resulted in the complete IPC removal and re-application; a very costly procedure.
Conventional Hardbanding
Fig. 1 shows a schematic of a worn hardbanding cross section exposing the hardbanding weld deposit, base metal HAZ and original tool joint material. The previous Duraband NC has worn flush to the tool joint surface. If the Duraband NC was applied correctly, the base metal HAZ should be less than 40Rc. This is acceptable. If exactly the same procedure is used for re-application with a 400°F (204°C) preheat and slow cool down, the base metal HAZ would fall within the specification of 40Rc hardness, but the IPC would be permanently damaged. The work-around for this is CoolBanding.
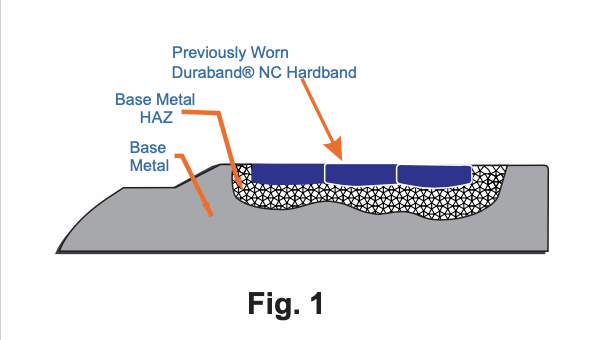
CoolBanding Explained
To understand how CoolBanding allows the IPC to be protected while at the same time does not violate the specification of the base metal HAZ hardness, it is essential to look at the parameter changes that will accomplish this.
Fig. 2 illustrates the difference the welding parameters have on the depth of penetration. 2A is a conventional setup with Electrode Positive with oscillation. 2B illustrates the HAZ effect if the oscillation is turned off or at zero, and 2C shows the oscillation at zero with Electrode Negative. It is clear that 2C is the most desirable.
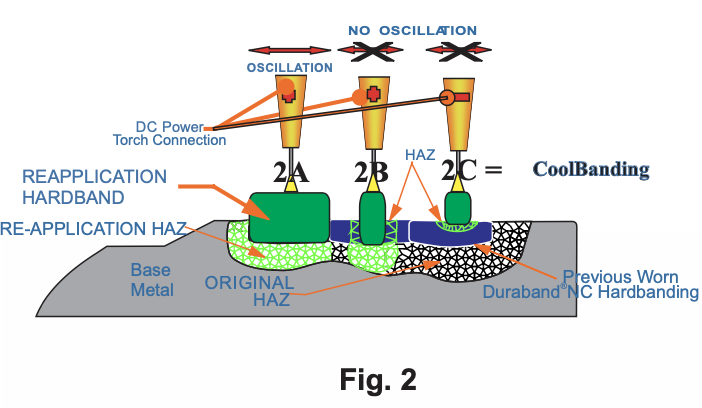
Fig. 3 shows a cross section illustration of the CoolBanding weld deposit. Welding with Duraband NC with Electrode Negative power connection and with no oscillation, results in very low penetration and dilution. Coupled with starting with a preheat of 150°F (66°C) and spraying heated water under the hardband area while welding, will protect the IPC. You may be asking, “but what about the base metal HAZ?” The operative word here is “base metal”, because this is what the original specification was concerned with. As shown in Fig. 3. the HAZ for the CoolBanding re-application is well inside the previous Duraband NC weld deposit and NOT associated with the base metal HAZ. In reality the base metal is actually tempered back by the CoolBanding deposit to a lower hardness than the original or previous hardbanding. This is an added advantage to the CoolBanding procedure.
Slow cooling procedures are still required for the CoolBanding procedure to help minimize the difference in shrinkage rates between weld metal and base metal. Slow cooling also promotes stress reduction.
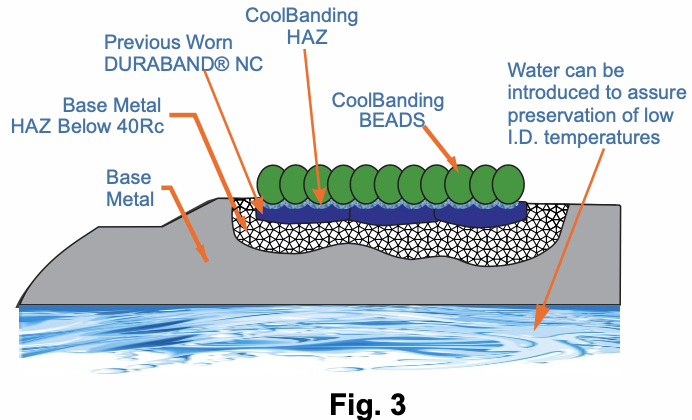
Hardness Profile
The hardness profile, Fig. 4 was taken through a section of a Coolband re-application deposit and
deep into the base metal. Tracks 1, 2 and 3 are the hardness indentations in the various zones from the CoolBanding, previous Duraband NC, base metal HAZ and finally into the base metal itself. It is interesting to note the drop in hardness in the previous Duraband NC. Under conventional hardbanding procedures the hardness is typically in the high 50’s to low 60’s Rc. This drop into the low 50’s Rc indicates that during the CoolBanding procedure, the heat from the bands actually tempered the previous Duraband NC layer. This heat carried a short ways into the base metal HAZ, which as shown is a slight dip in hardness into the mid 20’s and as the heat faded, the HAZ returned to normal hardness values.
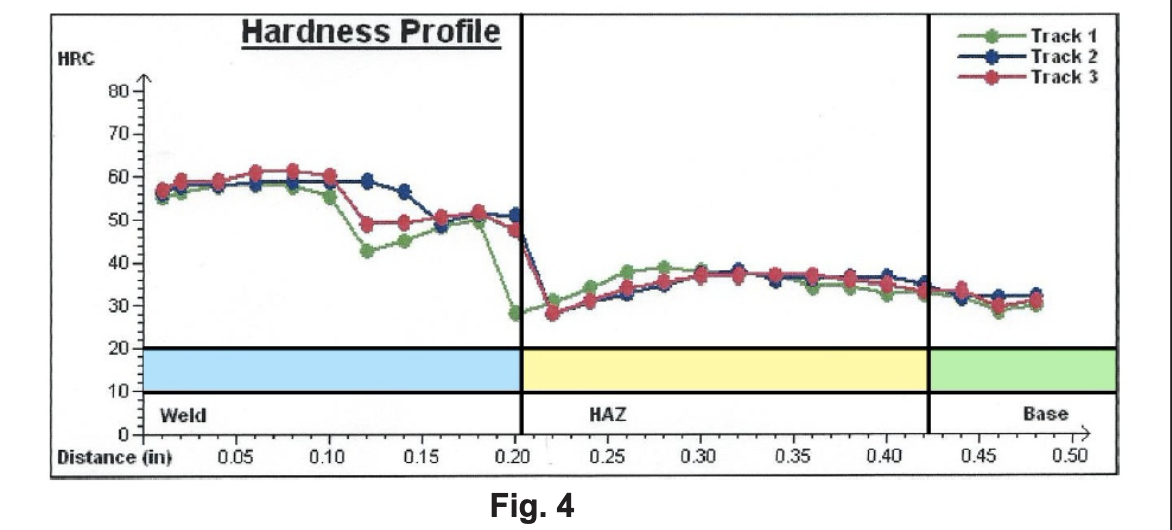
Summary
Conventional hardbanding procedures almost guarantee IPC damage from the heat of the welding arc combined with typical preheat and interpass temperatures. Furthermore, introducing cooling water at various temperatures almost guarantees violating maximum hardness values in the base metal HAZ. There is an alternative to these destructive procedures...CoolBanding. The CoolBanding re-application procedure over previously applied Duraband NC, was developed by Hardbanding Solutions by Postle Industries with the intent to protect the IPC from damage occurring during the re-application procedure providing the IPC was not damaged prior to the CoolBanding procedure.
While there are a few slight changes to the welding parameters, conventional hardbanding equipment can easily be used. Water spray must be utilized for successful IPC protection. Special Training and Certification are required to be able to use the CoolBanding re-application procedure over previously applied Duraband NC.