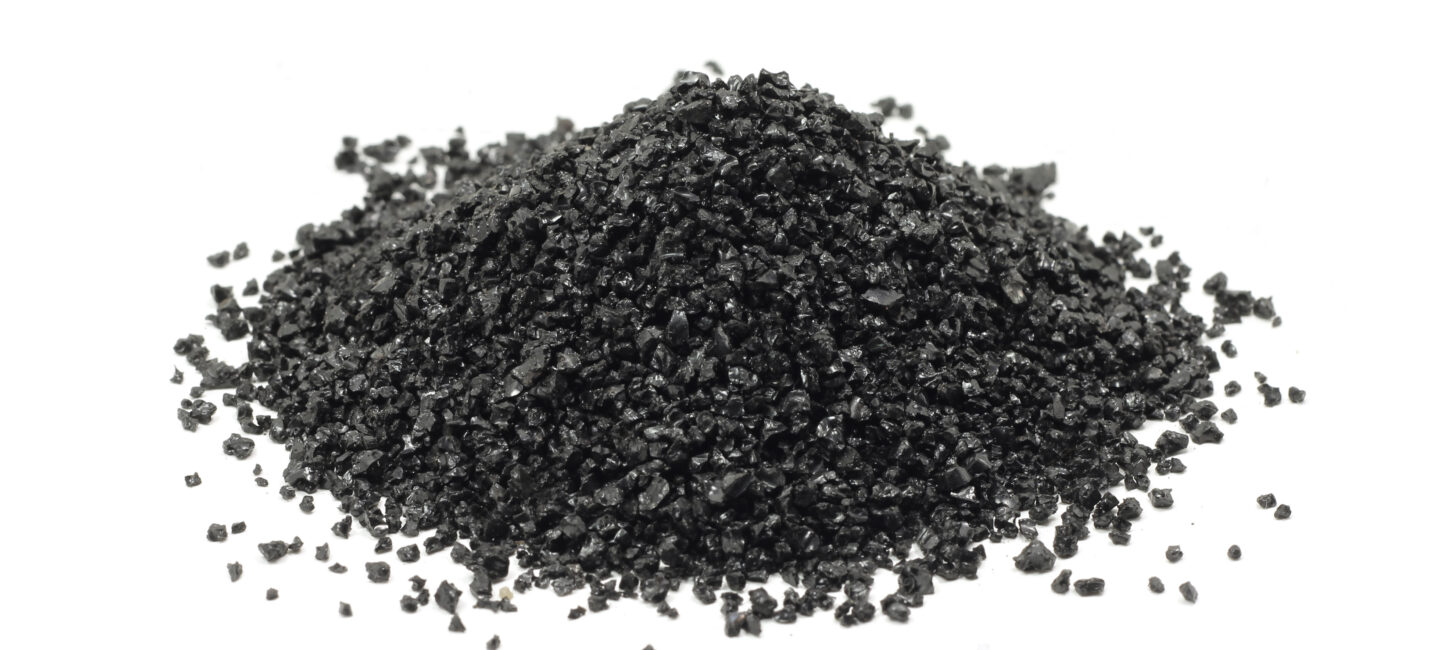
Hardbanding with Tungsten Carbide
Here you will find your options and our recommendations regarding tungsten carbide applications on your assets. Tungsten carbide in any form is not casing friendly. However, on occasion when contact with casing is not a concern, using tungsten can bring great benefits when drilling in abrasive conditions.
There are two different types of tungsten carbide, spherical and granular. It is applied into a welding matrix puddle to increase wear resistance.
Granular tungsten is around half the cost per lb. of spherical. Even though spherical is not casing friendly, it does provide less impact to casing on pass through as it is smooth compared to jagged and sharp cutting edges. It also provides an improvement in delivery in the welding process to provide a higher concentration of tungsten carbide pellets, due to the shape of the material which allows it to be compressed more in the matrix. Round pellets fit more tightly together than jagged sharp pieces providing more material for longer wear protection.
The wire used to create the matrix itself plays even greater part in the overall protection as it holds the carbide in position to provide wear resistance. A soft matrix such as mild steel with low wear resistance actually wears so fast that the carbide particles are released and provide little performance in wear resistance. The carbide essentially falls out as the matrix wear around it before providing significant protection.
Duraband is an excellent matrix. It provides high impact and wear resistance with good reception to carbide embedding. Tuffband is also a consideration as it receives carbide particles well, but does not share the wear resistance of Duraband.
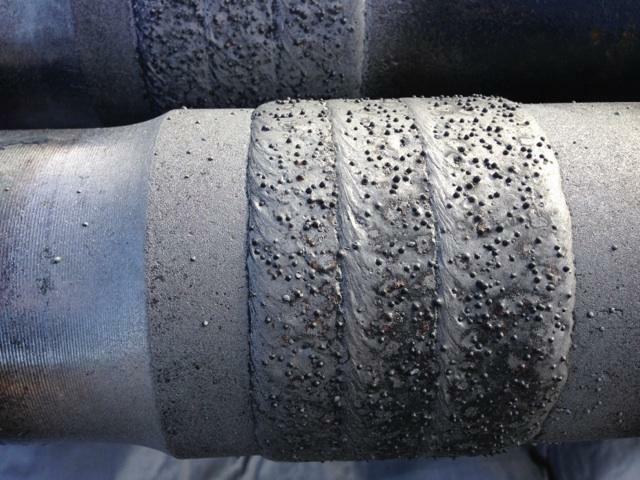
Tungsten carbide in Tuffband NC
The other important issue is the proper delivery of the carbide into the matrix. If carbide sinks too much it all accumulates at the bottom giving little wear protection and can cause issues of spalling at the fuse line of the weld. If delivery is only to the surface then it wears off quickly and provides only short term wear performance. Duraband and Tuffband provide a constant firm weld puddle that allows carbide to sink slowly with good saturation from top to bottom of the weld. It's important to apply in a way that gives saturation on the top 80% of the weld bead, so after the application is worn to reapplication height, the remaining matrix is not still saturated with carbide. This allows the next application to be applied back to casing friendly Duraband, or with reapplication using tungsten carbide again without removal or chance of porosity in the application, caused by welding over tungsten. The dispersion of carbide can be checked and monitored by spot check grinding at intervals to provide consistent results.
The final option would be an a slightly raised band of Duraband next to the tungsten application to provide protection in casing on pass through. On application the last band would not receive tungsten carbide and be applied as a slightly increased height to prevent contact of tungsten carbide to casing. This could be done on the last band of box application or an increased height of casing friendly on the pin, so the increased outside diameter doesn't interfere with elevators. Drill string maximum OD allowances would control criteria on this dimension. This is a temporary band for protection of casing until tools hit the open hole where it would wear down and Tungsten carbide would go to work providing the highest wear protection. After open hole use the Tungsten application is worn smooth for removal on trips. These options have proven to provide the highest protection in extreme environments with attention to casing protection. Communication with customer and no-go gauges to confirm maximum outside diameter are essential.
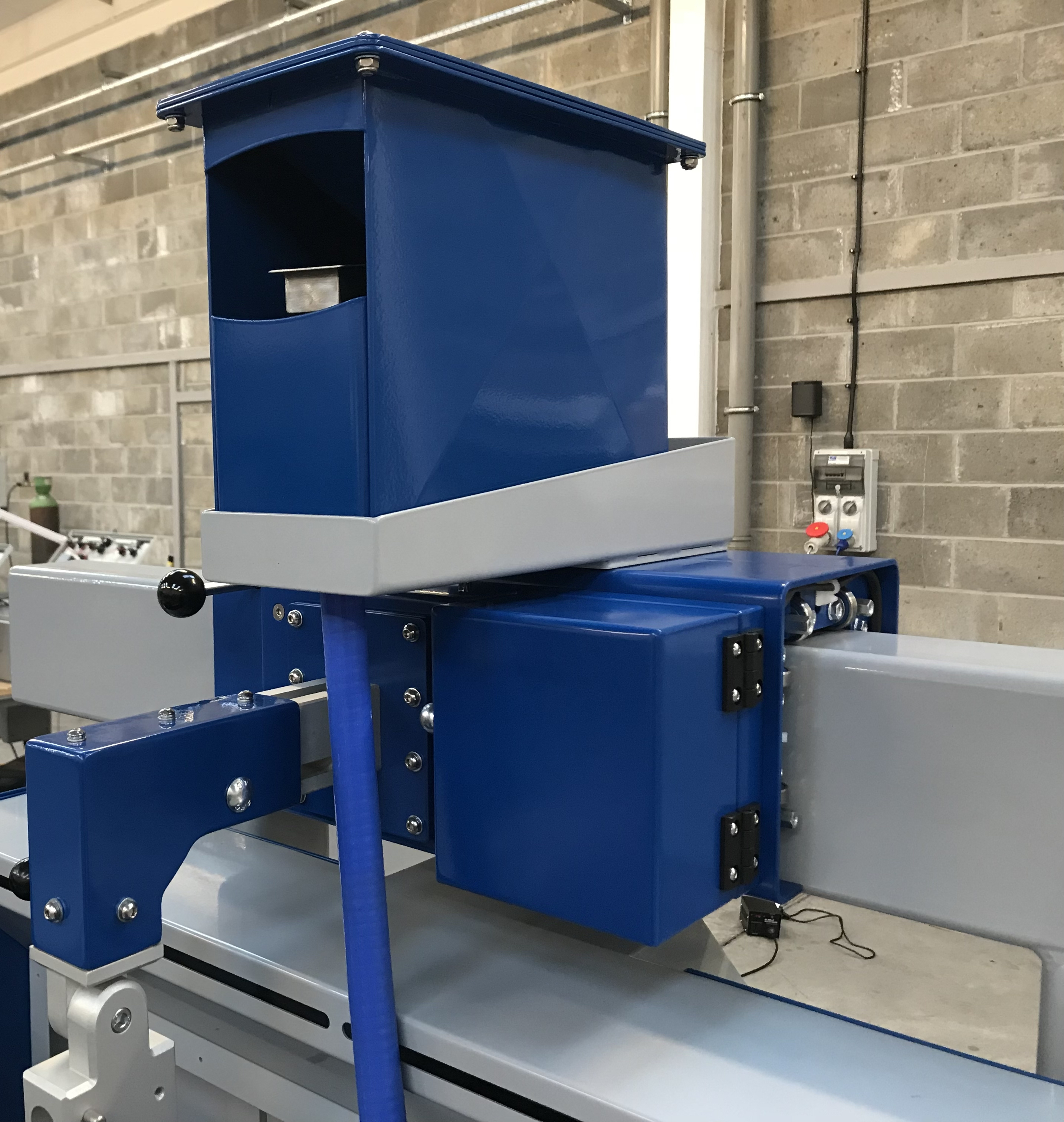
Vibratory tungsten hopper on a Skye hardbanding machine